- 건설에 9만3000여 명, 운영에 7만8000여 명 고용창출 효과
- 2011년 완공되면 세계 10위권 글로벌 철강기업 발돋움
- 해외에서도 관심 끈 세계 최초 밀폐형 원료 처리시스템
- 생산과정에서 발생하는 배기가스, 열기, 각종 부산물 100% 재활용
- 현대차그룹 자체적인 자원순환형 사업구조 구축
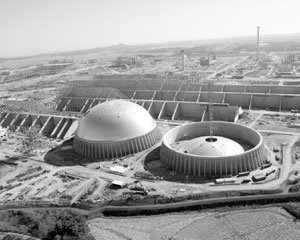
세계 최초로 만들어지는 밀폐형 원형저장고와 선형저장고.
충남 당진군은 현대제철을 비롯해 현대하이스코, 동부제강, 동국제강, 환영철강, 휴스틸 등 대형 철강제조업체들이 밀집해 있는 곳이다. 제조업체도 570개에 달한다. 경북 포항과 함께 우리나라의 대표적인 철강산업벨트라 부를 만하다. 그래서일까, 적어도 이곳은 요즘 세계를 뒤흔들고 있는 ‘경제위기’ 풍랑에서 한발 비켜나 있는 듯하다. 지역 주민에 따르면 총인구 14만에 불과한 이곳에서 100여 개 에 달하는 룸살롱이 성업 중이라고 한다.
2004년 한보철강 당진공장을 인수, 운영 중인 현대제철은 기존 공장 옆에 2011년 완공을 목표로 ‘세계 최초 친환경 일관제철소’를 건설 중이다. 2006년 10월27일 첫 삽을 떴으니 만 2년이 지났다. 친환경 제철공장이 가능한가 하는 궁금증과 얼마나 큰 규모일까 하는 호기심을 안고 공사 현장을 찾았다. 정문에 들어서니 짭조름한 바닷바람과 함께 쿵쿵 기계 돌아가는 소리가 활기차게 다가왔다.
현대제철은 국내 최대, 세계 2위 수준의 ‘전기로’ 철강회사다. 이곳 당진과 인천, 포항 공장에서 고철을 녹여 연간 1340만t의 철강제품(철근, H형강 등)을 생산하고 있다. 하지만 여기에 만족하지 않고 ‘제2의 도약’을 위해 고철이 아닌 철광석으로 고급 철강재를 만드는 일관제철소를건설하기 시작했다.
철은 크게 두 가지 방법으로 만들어진다. 광산에서 캐낸 철광석과 유연탄(원료탄·코크스)을 이용해 만드는 고로 제철법(blast furnace)과 철스크랩(고철)을 전기로를 이용해 만드는 전기로(electric arc furnace) 제강법이다.
전기로에서 고철을 녹여 만든 철강재는 표면상태보다는 강도 등을 요구하는 철근, H빔 같은 건설자재로 주로 사용한다. 반면 철광석에서 순수한 쇳물을 만들어 제품을 생산하는 고로제철법을 적용한 철강재는 표면이나 강도에 최고수준을 요구한다. 아주 미세한 흠집만 있어도 소비자가 외면하는 자동차나 고강도 고장력의 물리적 성질을 요구하는 선박용 후판 등이 주요 수요처다.
고로 제철에서도 일관제철은 ‘꿈의 제철’로 불린다. 철광석에서 여러 가지 강재가 만들어지기까지는 크게 나누어 쇳물을 만드는 제선, 쇳물의 불순물을 제거해 깨끗한 성분으로 만드는 제강, 원하는 형태의 철강제품을 만드는 압연의 3단계 공정을 거치게 된다. 이런 공정이 하나의 장소에서 한 번에 순차적으로 이뤄지도록 하는 게 일관제철이다. 생산 능률을 높이고, 수송비를 절약하고, 열효율을 좋게 하는 등의 효과를 얻을 수 있다. 우리나라에서 일관제철소는 포스코가 유일하다.
미래 성장동력
현대제철 일관제철소는 건설비용만 총 5조8400억원에 달한다. 건설인력 700만 명, 건설장비 48만6000대, 콘크리트 타설 물량 228만5000㎥가 투입된다. 연세대학교 도시교통과학연구소는 일관제철소 건설과 관련한 직간접 생산 유발효과가 13조원, 이후 제철소 운영에 따른 생산 유발효과가 연간 11조원에 달할 것으로 추산했다. 또한 건설에 따른 직간접 고용창출 효과가 9만3000여 명, 제철소 운영에 따른 직간접 고용창출 효과가 7만8000여 명에 달할 것으로 분석했다. 서해안고속도로, 인천국제공항 등 웬만한 국책사업보다도 더 큰 규모인 셈이다.
현대제철 홍보팀 장영식 과장은 “일관제철소 사업은 현대제철의 미래 성장동력이 고용창출과 철강 수요산업 경쟁력을 높이는 ‘국가적인 사업’이다. 일관제철소가 완공되면 연간 1700만t에 달하는 철강 원자재 수입물량 가운데 800만t을 대체해 5조원 이상의 수입대체 효과가 예상된다. 철강재 무역역조 개선에 많은 도움이 될 것이다”라고 자신했다.
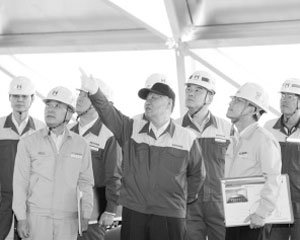
정몽구 회장은 공사 진척 상황에 각별한 관심을 보이고 있다.
일관제철소 건설 현장을 둘러보는 데 자동차로 이동했는데도 2시간 가까이 걸렸다. 총 135만평(약 446만㎡)으로, 기존 ‘전기로’ 공장의 부지(89만평)까지 합하면 224만평(약 740㎡)에 달한다고 한다. 여의도의 2.5배 면적이다.
현장에선 덤프트럭들이 끊임없이 오가고, 철근을 조립하는 인부들의 이마에는 제법 추운 날인데도 땀이 송글송글 맺혀 있었다. 현장 관계자는 “현재 고로 1호기를 기준으로 53%, 2호기까지 합치면 종합공정률이 40%를 넘어섰다”고 설명했다. 둘러보니 ‘뼈대는 다 갖추었고 이제 살만 붙이면 된다’는 말이 실감이 났다.
내년부터 철광석과 유연탄 등 제철원료 하역에 사용될 항만은 매립, 호안공사, 콘크리트공사가 거의 끝나는 등 98%의 진척률을 보이고 있다. 이제 뒷마무리만 하면 되는 셈이다. 항만은 길이가 1360m에 달하는데, 3만t, 5만t, 10만t과 20만t 선박이 정박할 수 있는 4선석(배가 육지에 닿는 부두)으로 이뤄진다고 한다.
일관제철소의 상징인 고로는 현재 1호기의 고로 본체를 구성하는 10단 철피 설치가 완료된 상태다. 그 옆에선 고로 2호기 기초공사가 한창이었다. 지반을 강화하기 위해 곳곳에 콘크리트 기둥을 지하 30m까지 박고 있는 광경이 눈길을 끌었다.
고로(高爐)는 철광석과 유연탄 등 제철원료를 이용해 철강제품 생산의 기본이 되는 쇳물(粗鋼·crude steel)을 생산하는 것으로 일관제철소 핵심설비다. 이곳에 들어서는 고로는 국내 최대 규모로 연간 400만t 이상의 쇳물을 생산할 수 있다. 본체는 최대 직경 17m, 높이 50m이며 공장이 완료되면 부대설비를 포함해 높이가 110m에 달한다고 한다. 5300m3급으로 기존 국내 최대인 포스코 광양제철소의 3800m3급보다 생산성이 30% 이상 높은 수치다.
2011년 2호기 고로까지 완성되면 열연강판 650만t과 조선용 후판 150만t을 생산할 수 있다. 이렇게 되면 전체 생산량이 연간 1900만t으로 늘어나 세계 10위권 글로벌 철강기업으로 성장하게 된다.
이외에도 유연탄과 철광석 등 제철원료를 처리하는 코크스공장과 소결공장, 쇳물의 성분을 조정하는 제강공장, C열연공장과 후판공장도 조금씩 그 위용을 드러내고 있었다.
밀폐형 제철원료 처리시스템
현대제철 당진공장 총무팀 이승희 대리는 일관제철소의 가장 큰 특징에 대해 “세계 최고 수준의 친환경 제철소를 지향한다는 점”이라고 강조했다. 이를 위해 선진국에서 검증된 최적의 환경기술로 오염물질 배출을 최소화하는 것은 물론, 발생된 오염물질 역시 최적의 관리시스템으로 제거하는 사전 설계방법을 적용했다고 한다.
“일관제철소의 대표적 오염물질로 지적되는 비산먼지를 원천 제거하는 ‘밀폐형 제철원료 처리시스템’을 세계 최초로 도입했습니다. 이 시스템은 밀폐형 연속식 하역기와 밀폐형 벨트컨베이어를 이용해 선박하역에서부터 원료처리시설까지 철광석과 유연탄을 운송함으로써 제철소의 가장 큰 오염물질로 지적되는 비산먼지 문제를 원천적으로 해결합니다. 또한 기존 개방형 원료처리시설에 비해 원료 적치 효율이 높고 기상 조건에 따른 운전 제약이 없어 원료 관리비용이 절감되는 등 일석이조의 효과를 얻을 수 있습니다.”
철광석과 유연탄 등 제철원료 저장소 역시 밀폐형으로 짓고 있다. 현재 원형(圓形)저장고 5동과 선형(線形)저장고 8동 등 총 13동의 원료저장고가 건설되고 있다. 지난 9월8일 첫 번째 원형저장고 돔 지붕을 상량했다. 돔 지붕은 지름 120m, 높이 60m의 거대한 규모로 야구장만하다. 현장에선 두 번째 돔 지붕 제작이 한창이었다. 원형저장고와 선형저장고를 합칠 경우 철광석 190만t, 석탄 130만t 등 약 45일분의 제철원료를 보관할 수 있다고 한다.
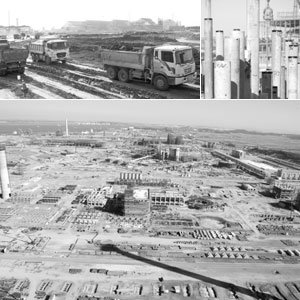
지반을 단단하게 하기 위해 콘크리트 기둥을 박고 있다(위 오른쪽 사진). 소결공장을 중심으로 본 일관제철소 공사 현장(아래 사진).
“이와 함께 철강제품 생산과정에서 발생하는 배기가스와 오폐수를 최적의 환경기술로 처리함으로써 원료의 저장에서부터 제품생산 후 폐기물질의 처리까지 완벽한 친환경 제철소를 구축할 계획입니다. 배기가스의 경우 TMS(Tele-Monitoring System·굴뚝자동측정장치) 설치를 통한 실시간 모니터링으로 오염 정도를 항상 감시, 관리할 수 있도록 할 예정입니다.”
비산먼지와 함께 환경문제로 제기되는 대기오염물질이 소결공정에서 발생하는 배기가스다. 이를 해결하기 위해 현대제철은 미세먼지는 전기집진기로, 황산화물(SOx)과 같은 가스상 오염물질은 흡착탑과 백필터로 이루어진 설비로 1차 제거한 후 2단 활성탄흡착설비를 이용해 황산화물, 질산화물(NOx), 다이옥신 등을 처리하는 시스템을 갖출 예정이라고 한다. 2단 활성탄흡착설비는 독일에서 입증된 최신 기술로 이 기술을 적용하면 배기가스 농도를 법적 규제치보다 훨씬 낮추어 방출할 수 있다.
오폐수 또한 화학반응조와 생물학반응조 등을 통해 1차 처리를 한 다음 활성탄흡착설비를 포함한 고도처리시설을 통과하게 함으로써 재이용률을 최대화하도록 설계됐다고 한다. 또한 이런 과정을 거쳐 오염물질이 제거된 물은 해안에서 300m 떨어진 심해에 방류함으로써 해양오염 방지에도 힘쓸 예정이라고 한다.
현대제철은 최신 환경설비를 도입해 환경오염물질을 제거하는 한편 자체적으로 발생하는 에너지와 부산물의 재활용을 통해서도 녹색 경영을 실천한다는 방침을 세웠다. 일관제철소는 흔히 에너지 소비량이 많은 것으로 알려져 있지만 사실 어느 공장보다 에너지 재활용률이 높은 곳이다.
이승희 대리는 “주요 생산공정에서 발생하는 각종 가스와 열기를 최대한 수집해 자체 발전소를 가동하는 동력으로 활용하거나 기체를 데우는 데 사용한다”며 “특히 고로와 코크스설비, 제강설비 등에서 발생하는 고온의 부생(副生)가스를 활용해 시간당 321MW의 전력을 생산할 수 있다. 이를 연간 생산 전력량으로 환산하면 무려 280만MWh에 달한다”고 강조했다.
100% 재활용
화석연료를 사용해 280만MWh의 전력을 생산하려면 연간 80만t에 달하는 석탄이 소요되며 이로 인해 발생하는 CO2 양이 150만t에 이른다. 따라서 부생가스 발전을 통해 에너지 절감과 온실가스 감축이라는 두 마리 토끼를 잡게 되는 것이다.
에너지뿐 아니라 철강제품 제조공정에서 발생하는 부산물도 100%에 가깝게 재활용된다. 일관제철소 제조공정에서 발생하는 부산물은 일반적으로 콜타르, 조경유와 같은 화성(化成)부산물과 슬래그(slag) 부산물, 분진, 슬러지, 스크랩류다.
현대제철 일관제철소의 연간 조강 생산량인 800만t을 기준으로 코크스 화성공정에서 발생하는 콜타르, 조경유, 유황과 같은 화성부산물은 연간 18만t. 이런 부산물은 피치, 카본블랙, 벤젠, 톨루엔, 자일렌, 인산질 비료 같은 화학산업 분야의 원료로 전량 재활용된다. 또한 연주 및 압연공정에서 발생하는 분진과 슬러지, 스크랩류 등은 고로와 전로 등의 원료로 재활용된다.
“특히 고로 및 제강공정에서 발생하는 슬래그 부산물은 연간 354만t에 달하는데, 이것들은 슬래그 시멘트나 도로 노반재, 골재 등으로 재활용됩니다. 20평 아파트를 짓는 데 약 54t의 골재가 소요되는 것을 감안하면 354만t의 슬래그는 매년 20평짜리 아파트 6만5000가구를 짓는 데 소요되는 골재량을 대체할 수 있습니다. 골재 자원이 산림 파괴를 통해 생산되는 점을 고려할 때, 그만큼의 자연생태계를 보전하게 되는 셈입니다.”
이렇듯 환경을 강조하는 이유에 대해 현대제철 관계자는 “여기엔 세계 최고 수준의 제품 경쟁력과 함께 환경 분야에서도 최고의 기준을 만들어야 한다는 정몽구 회장의 강한 의지가 담겨 있다”고 설명했다.
자원순환형 사업구조
현대제철의 친환경 경영은 일관제철소 건설 이전부터 계속되어왔다. 기존의 ‘전기로’ 제강법 자체가 친환경적이기 때문이다. 철스크랩(고철)은 버려진 채로 방치할 경우 자연환경을 오염시킨다. 이를 수거해 전기로에서 녹인 후 새로운 철강제품으로 만들면, 이렇게 재활용된 철강 분량만큼의 철광석을 채굴하지 않아도 되기 때문에 환경파괴를 야기하지 않는다는 것.
1t의 철스크랩을 전기로에 넣어 제품화해 사용한 후 다시 수거해 제품화하는데 90% 이상이 회수된다. 따라서 1t의 철스크랩은 40회 이상 수거, 재활용되어 누적사용량이 무려 10t에 달하게 된다. 현대제철은 기존의 인천, 포항, 당진 등 3개 전기로 공장에서 연간 1100만t의 철스크랩을 재활용해왔다.
게다가 철스크랩을 녹이는 과정에서 부산물인 슬래그가 1t당 12~16% 발생한다. 연간 1100만t의 철스크랩을 재활용하므로 여기서 약 150만t의 슬래그가 발생하게 되고 이는 골재로 재활용된다. 자연에 버려진 채로 방치될 경우 환경오염을 일으키는 철스크랩을 재활용해 철강제품으로 재탄생시키고, 슬래그도 골재로 활용하는 자원 재활용업체로서 녹색 경영을 실천해온 셈이다.
현대제철 관계자는 “현대제철은 향후에도 경제적 성과뿐만 아니라 환경에 대한 책임과 지속가능한 발전에 대한 기여가 기업 발전의 원동력이라는 사실을 깊이 인식하고 녹색 경영에 최선의 노력을 다할 방침”이라며 “최신설비 도입으로 국제경쟁력을 높이는 한편 밀폐형 원료이송 및 보관설비 등을 완비해 친환경 제철소를 건설함으로써 녹색 경영을 선도할 것”이라고 강조했다.
한편, 2011년 일관제철소가 완공되면 현대차그룹으로서는 ‘쇳물(현대제철)-자동차용 냉연강판(현대하이스코)-자동차(현대·기아차)-폐차처리(현대차)-고철재활용(현대제철)’의 ‘자원순환형 사업구조’를 형성하게 된다. 현대기아차그룹 관계자는 “철강은 그 자체로 환경친화적인 소재인데, 이러한 ‘자원순환형’ 사업구조의 구축을 계기로 세계적으로 앞서가는 친환경그룹이 될 것”이라고 자부했다.